Mechanical Engineering
Our mechanical design division utilizes years of engineering experience to provide our partners with all facets of services – from research and development, specification and prototyping, to analysis services.
We virtually build entire models for clients, conducting testing and computational analyses at the design and prototyping stage, thereby limiting time, money, and waste during the manufacturing stage.
White Glove
Our deep team of engineers works hand-in-hand with all stakeholders throughout the entire product development process utilizing Modified Agile Hardware Development (MAHD), from conception and drawing to wireframing, prototyping, and testing - our methodology always keeps a user’s experience top of mind for our clients - including entrepreneurs, startups, mature companies, and governmental agencies.
We handle all the tough work allowing founders or businesses to focus on what they are good at with our transparent processes and methodologies allowing the knowledge gap to remain small or none at all.
À la carte
Our à la carte approach to mechanical engineering puts you in control. Whether you need a one-off analysis, detailed CAD work, prototyping support, or help navigating manufacturing constraints, we offer flexible, standalone services tailored to your specific project needs—no long-term contracts or bundled commitments required.
Prototyping
We’re an industry-leading, American-made rapid prototyping company providing high-quality prototypes (eg: 3d printed, resin cast, machined) from either provided CAD models or in-house designed components, which can help de-risk and optimize manufacturing process introduction.
Process Modeling and Simulation
Simulation is sometimes used interchangeably with modeling, but really, simulation is the result of running a model. The model comes first; that model is then used to perform simulation studies. Typically, you are using a model to either reproduce a historical period (for validation purposes) or to extrapolate data to predict the future (for what-if studies). You may perform many simulations with a single model exploring additional alternatives or replication with each simulation.
Reverse Engineering
Reverse engineering, sometimes called back engineering, is a process in which software, machines, aircraft, architectural structures, and other products are deconstructed to extract design information from them. Often, reverse engineering involves deconstructing individual components of larger products. The reverse engineering process enables you to determine how a part was designed so that you can recreate it. Companies often use this approach when purchasing a replacement part from an original equipment manufacturer (OEM) is not an option.
Tooling Design
Tooling design is an essential part of the manufacturing process. It refers to the plans and components used to build a product or part, from start to finish. This type of design covers everything from selecting raw materials and molding them into specific shapes to machining parts for accuracy and assembly processes.
Design For Manufacturing (DFM)
Tooling design is an essential part of the manufacturing process. It refers to the plans and components used to build a product or part, from start to finish. This type of design covers everything from selecting raw materials and molding them into specific shapes to machining parts for accuracy and assembly processes.
Product Design
Landi bridges the gap between ideas and productions. Often taking ideas from rough hand sketches or whiteboard creations outside of SolidWorks all the way into a fully integrated Product Lifecycle Management (PLM) system.
Improved Assembly & Inspection
We optimize your product's assembly and inspection processes to enhance efficiency, reduce errors, and ensure consistent quality. Our approach identifies opportunities to simplify mechanical interfaces, improve part orientation, and streamline fastening or joining methods—saving time on the floor and minimizing risk during production.
From fixture design to visual inspection guides, we integrate feedback loops between design and manufacturing to make sure every part fits right the first time, every time.
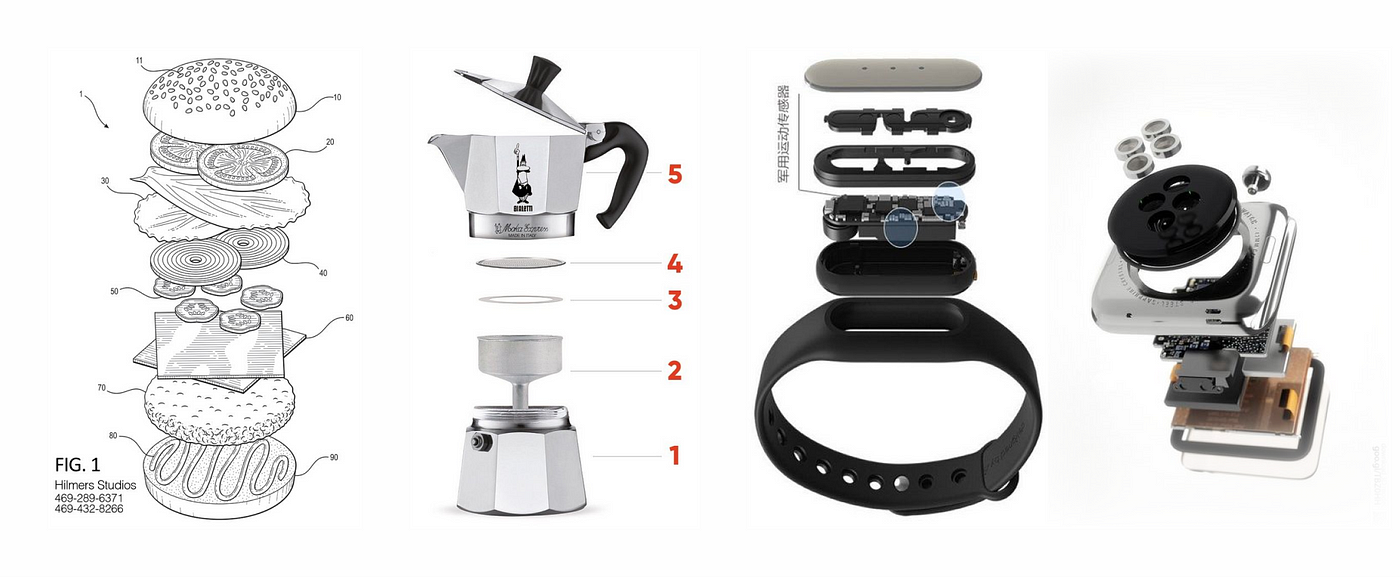